Functions of electromagnetic flowmeters
A electromagnetic flowmeter (abbreviation: EMF) normally comprises a measuring tube that comes into contact with the media and that has two electrically conductive electrodes, as well as magnets outside the measuring tube, the measuring electronics and the electrical connections to the electrodes. The components are surrounded by a sensor housing. If an electrically conductive fluid flows inside the measuring tube, the free charge carriers are deflected vertically to the magnetic field lines in the fluid due to the external magnetic field (Hall effect) and generate measurable voltage on both electrodes. The charge carrier deflection and the voltage generated by this are proportional to the medium’s flow speed, which can now be calculated based on the voltage. The flow rate can be determined finally from the speed and volume.
Electromagnetic flowmeters are only suitable for measuring conductive fluids or suspensions; gases and solids, as well as insufficiently conductive fluids cannot be measured using this technology.
The benefits of ceramic measuring tubes
Even though plastic is often used to make the measuring tube, a measuring tube made of ceramic has many clear benefits. The range of applications for electromagnetic flowmeters can be expanded dramatically by using ceramic measuring tubes, e.g. to measure highly corrosive or abrasive fluids. Using ceramic instead of plastic may even be beneficial in applications where corrosion or wear is not the main problem.
Ceramic materials are non-metallic, inorganic materials. From a chemical point of view, they comprise oxides, carbides, nitrides or borides of metals and their compounds. Their micro-structure is polycrystalline and can also contain amorphous (vitreous) parts. There is a wide range of ceramic materials with very different attributes, and the material should be selected according to the application. Nevertheless, the majority of these materials have certain attributes in common, such as their high degree of hardness and wear resistance, excellent corrosion resistance and massive temperature resistance. However, there is also a low degree of ductility (“brittleness”). Added to this, are certain design limitations (keyword: “suitable for ceramics”), as well as time-consuming production and the accompanying high price in comparison to metals and plastics.
As the only part that comes into contact with the fluid in this type of flow measurement is the measuring tube, its properties have a major influence on the range of applications the sensor can be used in. Kyocera ceramic measuring tubes are provided with the required electrodes using a special, patented sintering-in technique and, furthermore, do not contain any metallic or organic components such as solder or additives. We use our F99.7 (a high-purity aluminium oxide) and FZM (a zirconium oxide that is partially stabilised with magnesium oxide, known as Mg-PSZ) ceramics as our materials. Both are certified for use in the food industry. Thanks to our many years of experience in sintering in the electrodes, the measuring tubes are seamless and therefore easy to clean. The connection between the ceramic body and the electrode is completely free of leakages and remains so even if the temperature changes quickly, e.g. in CIP or SIP processes.
Thanks to the excellent wear, corrosion and pressure resistance of the ceramic materials used, flowmeters with ceramic measuring tubes can also be used under extremely demanding conditions, such as highly abrasive or corrosive fluids and high pressures. They are therefore clearly superior to plastic measuring tubes and open up fields of application in which this type of flow measurement was never used up to now.
A basic and general benefit of ceramic measuring tubes over plastic measuring tubes is their absolute resistance to deformation. Even the most modern, high-performance plastics become slightly deformed over time. If this deformation exceeds a specific limit, the flowmeter has to be re-calibrated. This step is not required when using ceramic measuring tubes.

Ceramic measuring tube with sintered-in platinum electrodes for magnetic-inductive flow meters
Sintering in and cermet technology at Kyocera
Either pure platinum pins or “cermets” can be used as the electrode material in ceramic measuring tubes. KYOCERA Fineceramics Europe GmbH has special and unique technology to sinter the electrodes in and to manufacture suitable cermet electrodes. This is an established procedure in our production processes and we have many years of experience with using these technologies.
The benefit of this joining method is that no further aids are required and therefore, the final product does not contain any metallic (apart from the platinum for the electrodes) or organic substances. Platinum is a precious metal with a similar level of corrosion resistance as ceramic and is protected against mechanical effects by the surrounding ceramic. Cermets are a mixture of ceramic and platinum (cermet = Ceramic & Metal), and have even better attributes as an electrode material than pure platinum. They are more resistant to corrosion and wear than platinum. Furthermore, the connection between the cermet electrode and ceramic is even more robust and withstands high pressure and fast temperature changes without problems.
When sintering in the cermet electrodes, diffusion processes between the electrode and the ceramic form a solid ceramic connection so that the joint zone is no longer a mechanical weak point. This is proven impressively in the mechanical load test, in which the measuring tube does not generally break at the electrode but in the middle of the ceramic structure.
Of course, this technology is also subject to certain limitations. Therefore, the electrodes must have as simple and round a shape as possible. Furthermore, sintering in is limited to relatively small electrode dimensions of several millimetres depending on the material. A minimum electrode length of several millimetres is required for a reliable and stable connection between the ceramic and the electrode.
Even though ceramic measuring tubes are significantly more expensive than plastic solutions, this investment is more than worth it in the long run thanks to the superior attributes, the reliability and the service life.
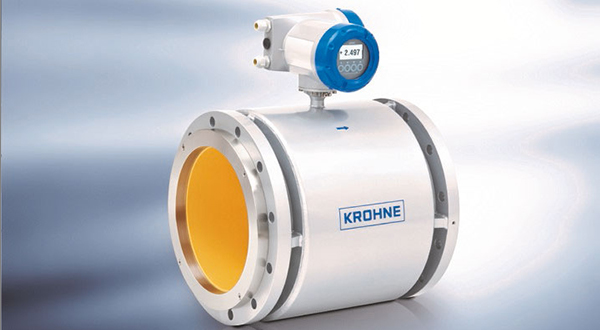
[1] Source: https://de.krohne.com/de/produkte/durchflussmesstechnik/durchflussmessgeraete/magnetisch-induktive-durchflussmessgeraete/optiflux-5300/
KROHNE, our partner of many years
The KROHNE Group is a leading specialist in the industrial process instrumentation sector and has relied on ceramic products from KYOCERA Fineceramics Europe GmbH for many years. KROHNE brought the first electromagnetic flowmeter with ceramic measuring tube and sintered-in platinum electrodes onto the market in 1981. This marked the beginning of an extraordinary partnership between KROHNE and KYOCERA Fineceramics Europe GmbH (formerly known as Friedrichsfeld GmbH, later FRIATEC GmbH), which still exists to this day. During this time, a wide range of joint developments took place, especially to the ceramic measuring tubes for the electromagnetic flowmeters, which KYOCERA continues to develop and improve.