Precision and design flexibility in a single step
3D printing of ceramic components by Kyocera
Ceramic 3D printing is revolutionising the production of complex high-performance components. In contrast to conventional manufacturing methods, additive manufacturing enables the creation of components with almost unlimited design flexibility - whether complex lattice structures, undercuts or topology-optimised geometries. This makes ceramic 3D printing the ideal solution for demanding applications where conventional manufacturing techniques reach their limits.
Thanks to our innovative process and high-quality ceramic materials, we can offer you durable high-precision components - from quick prototype development to series production.
The advantages of 3D printed components made from technical ceramics
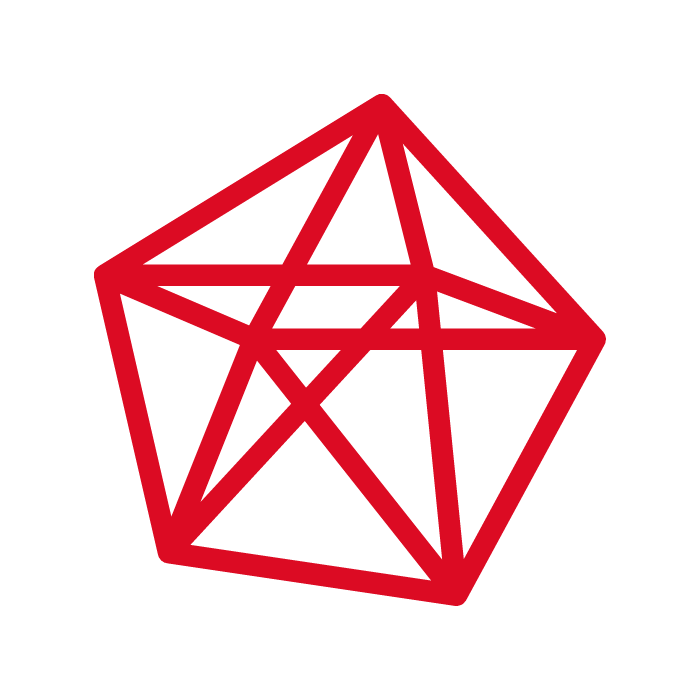
Complex geometries
Our process allows the production of even very complex structures.
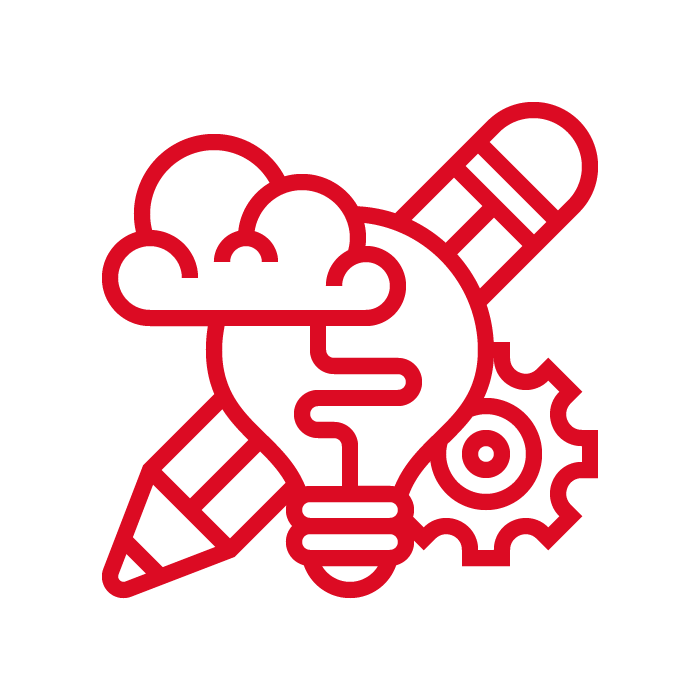
Design consulting
We support you in the design and development of topology-optimised components and lightweight structures.
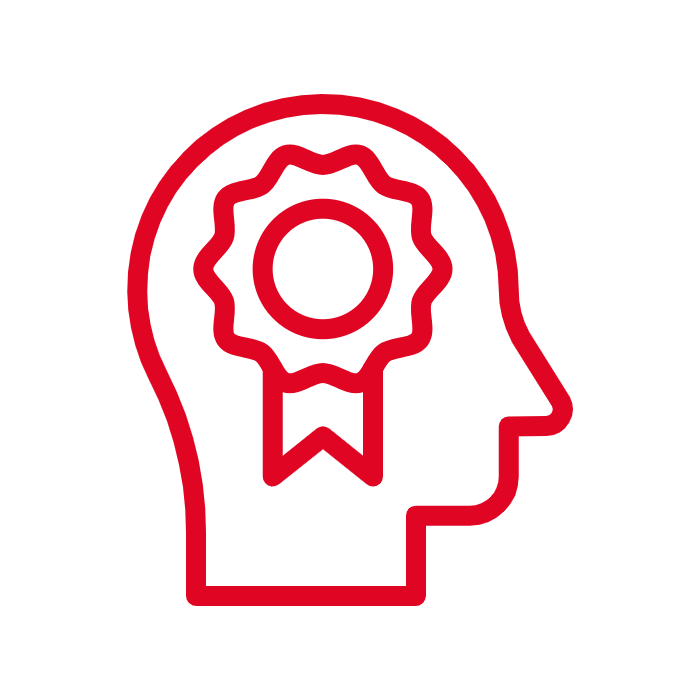
Process expertise
Thanks to our many years of expertise in the field of technical ceramics, we are able to offer coatings and finishes in addition to a homogeneous material.
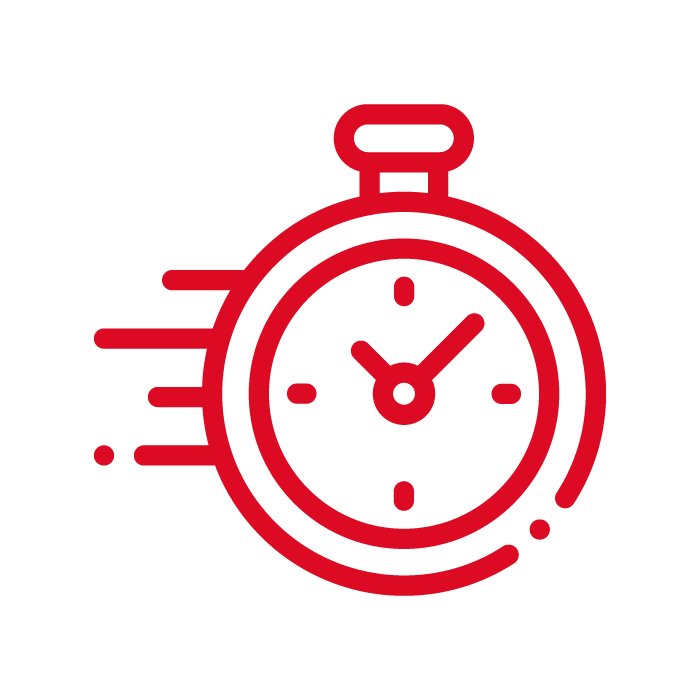
Short production time
The elimination of green machining enables fast production. Therefore, 3D printing is also ideal for prototype production.
3D printing of SiSiC components
Silicon infiltrated silicon carbide (SiSiC) is a high-performance ceramic material known for its exceptional mechanical strength, thermal stability, rigidity and wear resistance, making it ideal for applications in harsh environments such as aerospace, semiconductor manufacturing and industrial production processes. Like our SiSiC for conventional forming processes (StarCeram® Si), our SiSiC for 3D printing (StarCeram® AM-Si) is processed in-house and is comparable in terms of material properties.
With the advances in additive manufacturing technologies, 3D printing has proven to be a revolutionary approach for the production of complex ceramic SiSiC components. Compared to conventional forming processes such as isostatic pressing or slip casting, additive manufacturing offers greater design flexibility and shorter production lead times. 3D printing of SiSiC usually involves a two-stage process: first, a green part is printed from silicon carbide powder and a polymer binder with binder jetting. This green part is then infiltrated with molten silicon, which reacts with the remaining carbon to form the final SiSiC structure.
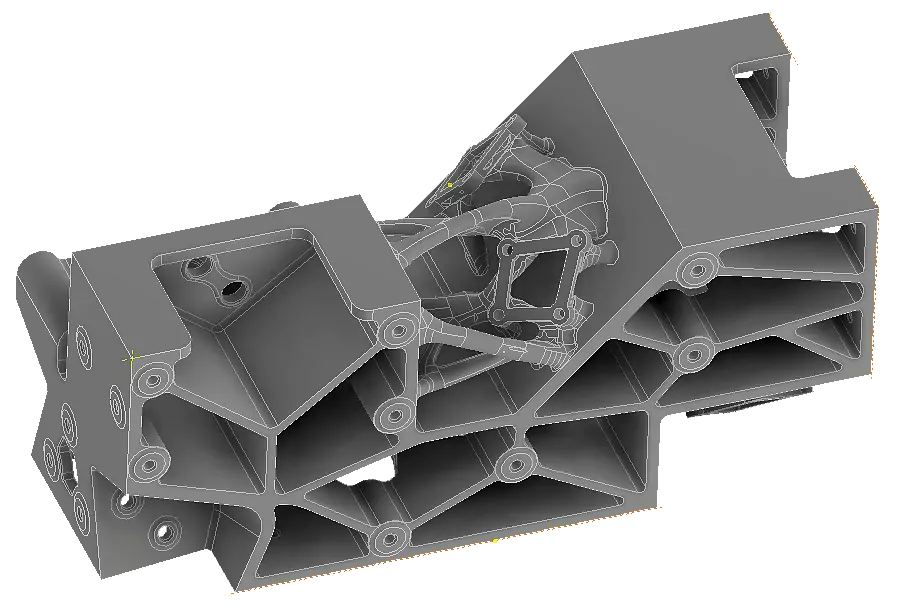
Material properties and specifications of SiSiC
Material properties
- High strength
- Excellent mechanical high-temperature properties
- Excellent thermal shock resistance
- Low thermal expansion
- Very high thermal conductivity
- High wear resistance
- Very high stiffness
Specifications of 3D-printed components
- Dimensions up to 325 x 270 x 130 mm
- Wall thickness > 3 mm
Comparison of the material properties of SiSiC
Property | StarCeram® AM-Si (3D printed) | StarCeram® Si |
---|---|---|
Density [g/cm3] | 3 ± 0.03 | 3.05 |
Flexural strength [MPa] | 190 | 300 |
Weibull Modulus | >10 | >10 |
E-Modulus [GPa] | 350 | 380 |
Poisson's ratio | 0.19 | 0.18 |
Mean coefficient of linear thermal expansion [10⁻⁶/K] | 2.33 (0-40°C) | 4 (20-1000°C) |
Thermal conductivity [W/m‧K] | 185 | 180 |
Electrical conductivity [10⁻³MS⋅m] | 10 | 6 ± 1 |
Microstructue SiC content [%] | 75-80 | >85 |
Typical colour | Grey | Grey |
Learn how your application can benefit from additive manufacturing!
Your advantages with 3D printed ceramics from Kyocera
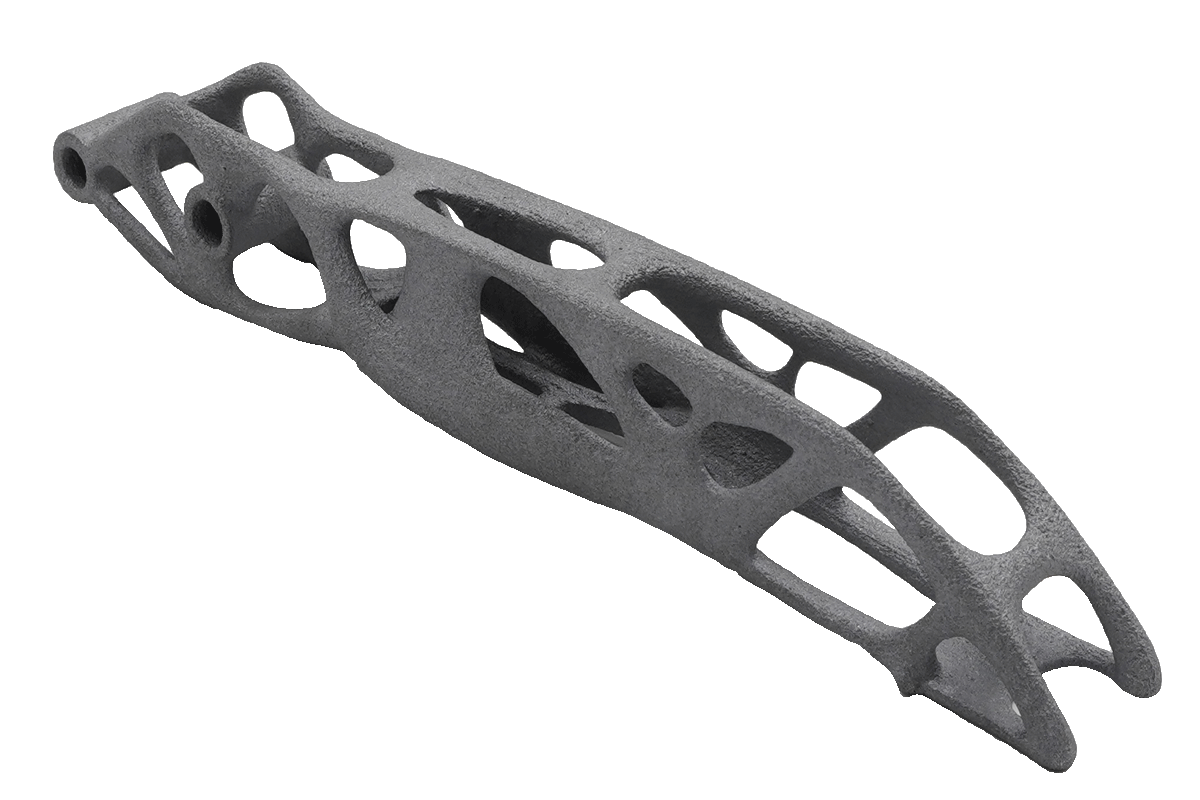
Production of complex geometries
The more complex the component, the greater the advantages of additive manufacturing compared to conventional forming processes.
3D printing enables the production of almost any geometry, including curved surfaces, undercuts, text and graphics and much more.
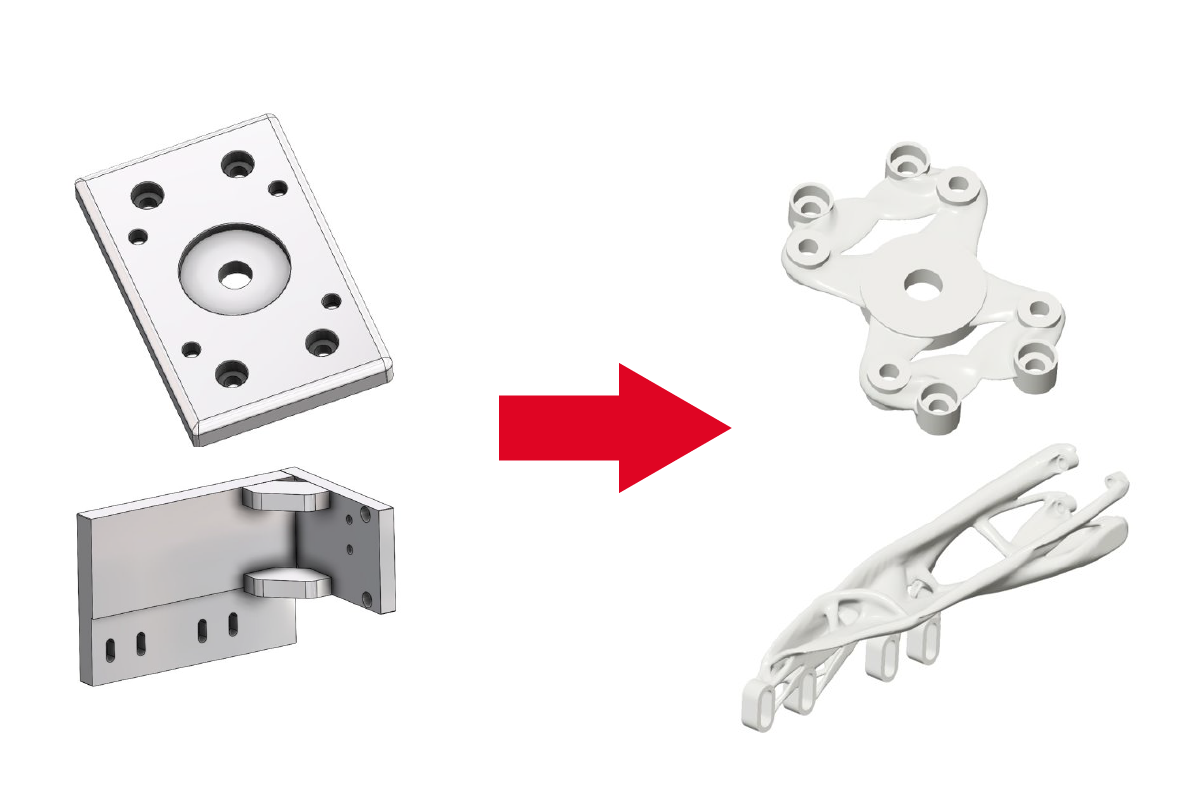
Design consulting
Our design centre supports you in optimising your components.
In contrast to conventional forming processes (CIP, HIP, etc.), there are hardly any geometric restrictions when 3D printing ceramic components. A significant weight reduction can therefore be achieved for components through topology-optimised design.
Our colleagues in the design centre will help you to find the best possible geometry.
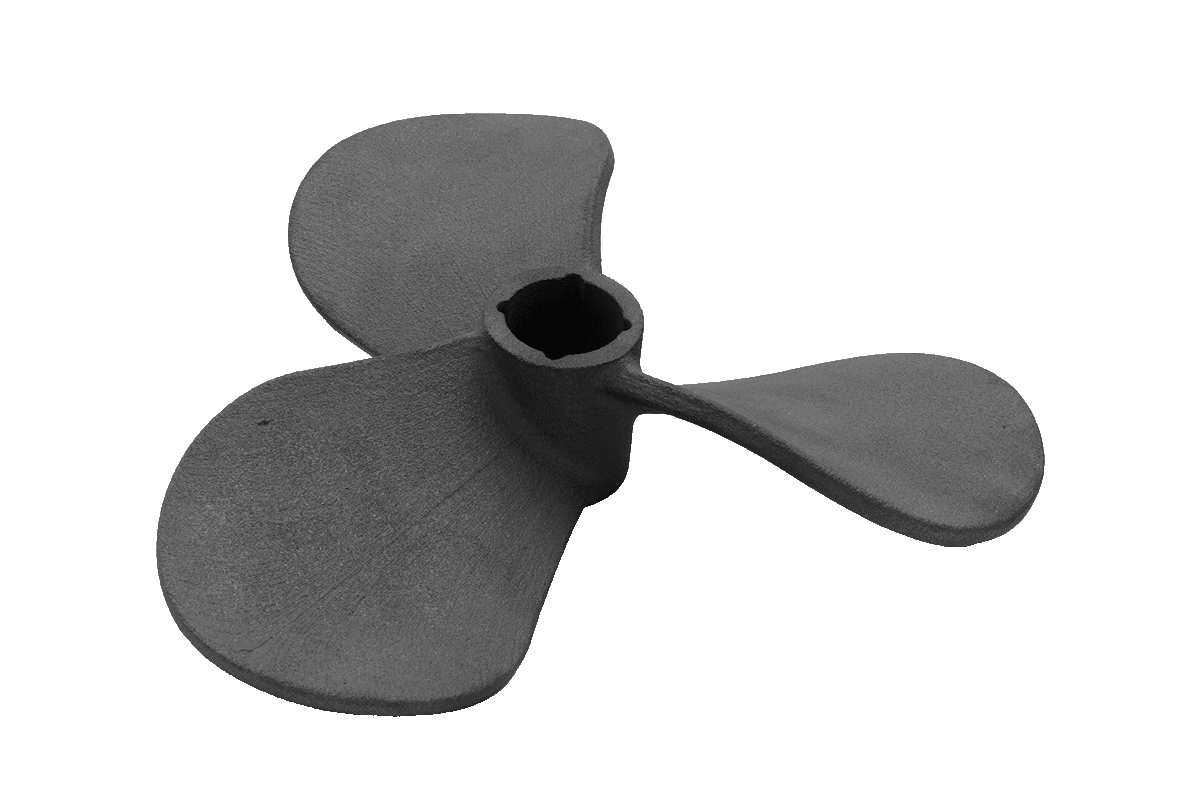
Process expertise
Kyocera has extensive expertise in the production and processing of technical ceramics. In addition to the development of homogeneous, high-purity materials, we have also mastered sophisticated post-processing and coating technologies that significantly expand the range of applications for our 3D-printed components.
Our continuous commitment to innovation is constantly driving the technology forward - this will also enable us to produce large-volume components in the near future. This combination of materials expertise, process reliability and vertical integration makes Kyocera a reliable partner for customised solutions in ceramic 3D printing.
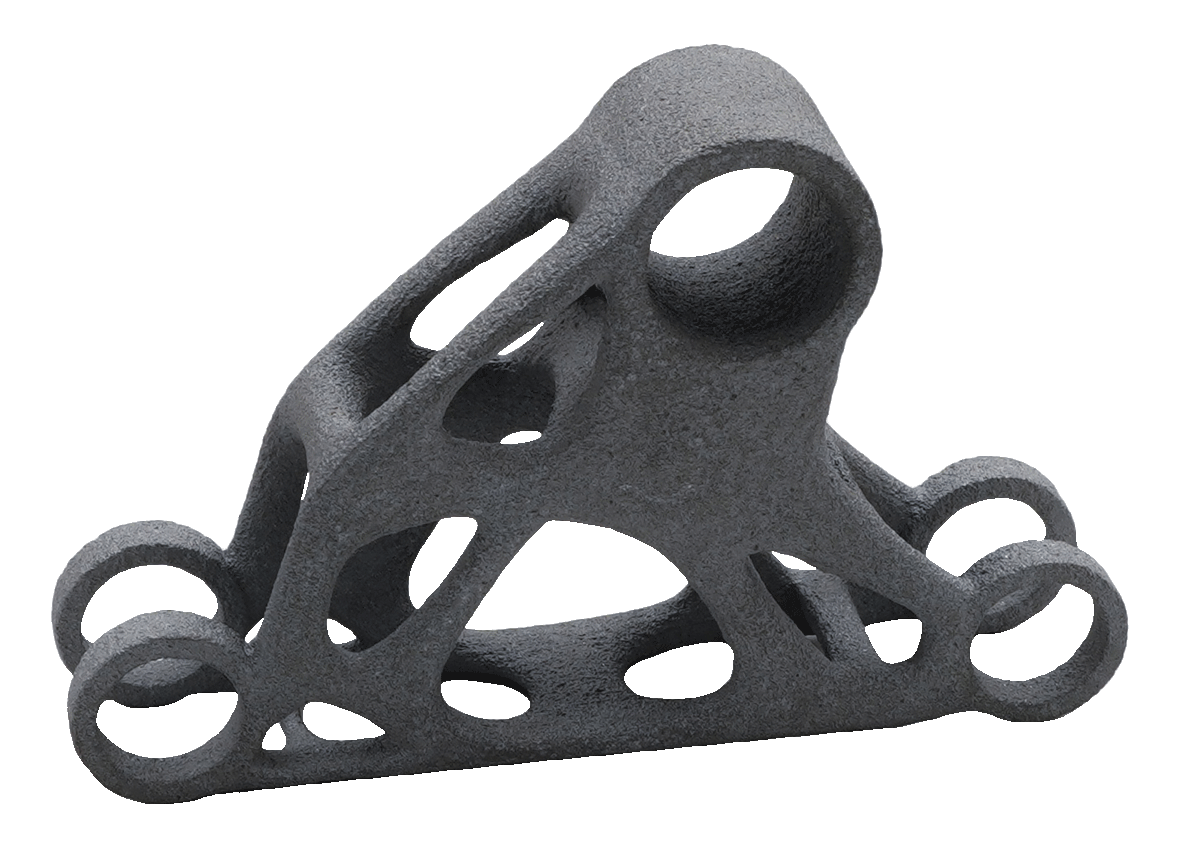
Time savings
With ceramic 3D printing, the green machining production step is completely omitted. This ensures short delivery times and makes additive manufacturing ideal for the quick production of prototypes. Larger quantities are also possible. Ceramic 3D printing offers significant advantages, particularly for components with complex geometries.
The process of ceramic 3D printing
Other materials for small-format 3D printing
In addition to the additive manufacturing of SiSiC, with which components up to a size of 325 x 270 x 130 mm can be realised, Kyocera also offers 3D-printed components made from other materials. These can be produced up to a size of 400 x 110 x 50 mm and allow wall thicknesses from 0.25 mm.
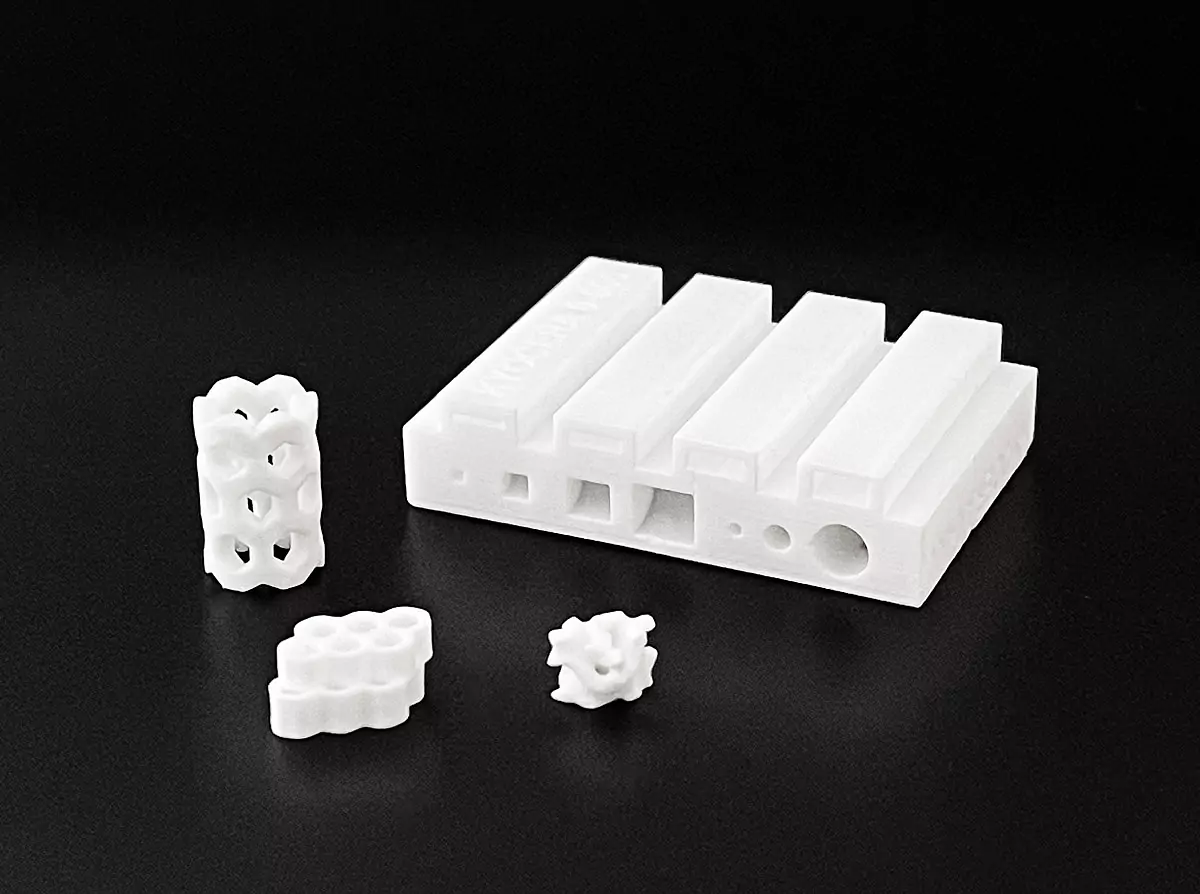
Alumina (Al₂O₃)
High-purity alumina (> 99.8 %) offers very good thermal conductivity, low weight and excellent electrical insulation properties. It has a high thermal shock resistance and is exceptionally stable at high temperatures. Its low dissipation factor makes it ideal for electronic and thermal applications.
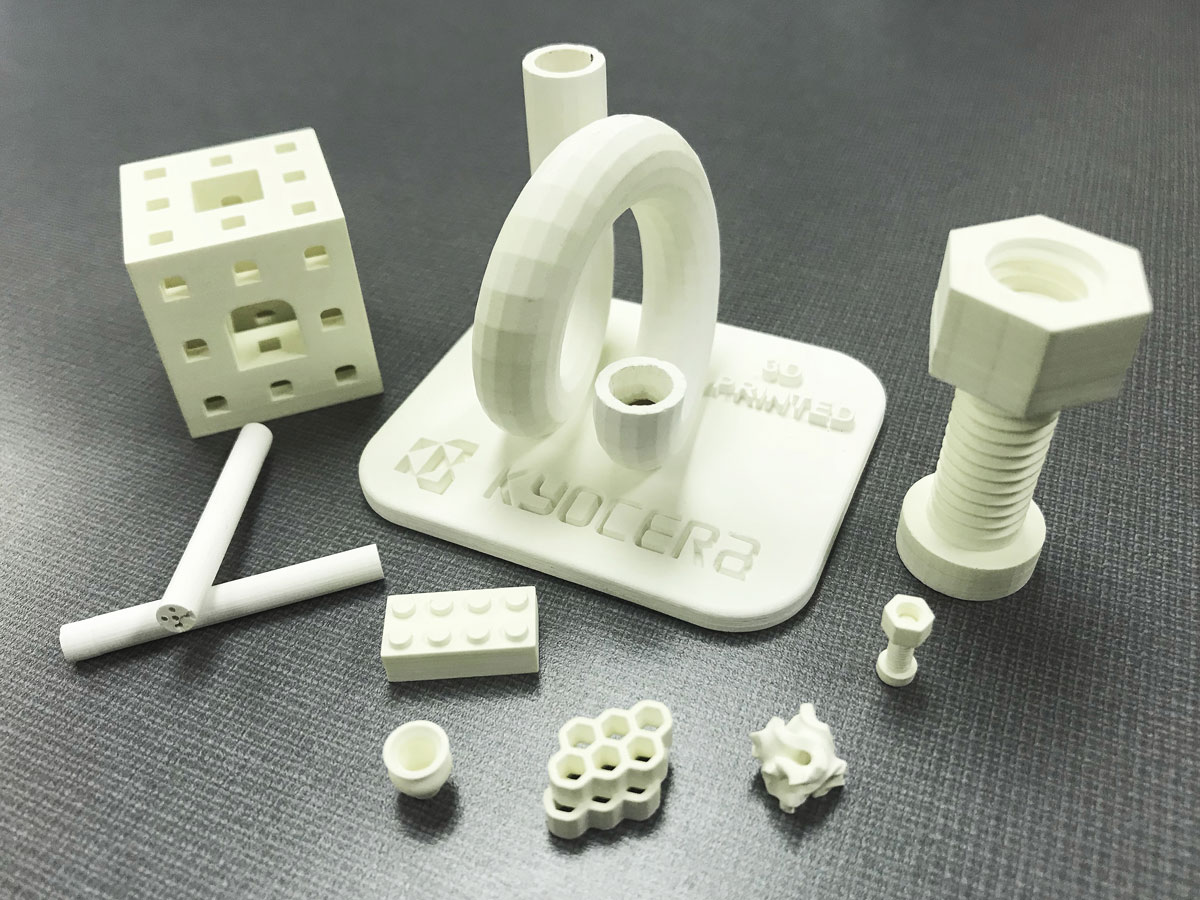
Zirconia (availability depends on quantity)
Yttrium-stabilised zirconia (YSZ) impresses with its exceptionally high wear resistance, toughness and chemical inertness. It exhibits excellent resistance to high temperatures - even when in contact with molten metals - and can be processed into mirror-smooth surfaces. Ideal for highly stressed, precise applications.
Comparison of the material properties of alumina and zirconia
Property | Alumina (3D printing) | Kyocera AO480S | Zirconia (3D printing) | Kyocera ZO201N |
---|---|---|---|---|
Density[g/m³] | 3.9 | 3.9 | 6.0 | 6.0 |
Vickers Hardness (HV9.807N) [GPa] | 16.2 | 17.2 | 12.3 | 12.3 |
Flexural Strength (3 P. B.) [MPa] | 460 | 480 | 1000 | 1000 |
Young's Modulus [GPa] | 387 | 380 | 215 | 200 |
Poisson's ratio | 0.23 | 0.23 | 0.31 | 0.31 |
Fracture Toughness (SEPB) [MPa√m] | 3.4 | 4.3 | 4.5 | 6.0 |
CTE 40 ~ 400 °C [⋅10⁻⁶/K] | 7.1 | 7.2 | 10.0 | 10.5 |
CTE 40 ~ 800 °C [⋅10⁻⁶/K] | 8.0 | 8.0 | 11.0 | 11.0 |
Thermal Conductivity (20 °C) [W/(m⋅K)] | 32 | 32 | 3 | 3 |
Specific Heat Capacity [J/(g⋅K)] | 0.78 | 0.79 | 0.46 | 0.46 |
Dielectric Strength [kV/mm] | 17 | 15 | 11 | 11 |
Volume Resistivity (20 °C) [Ω⋅cm] | >1.0E+14 | >1.0E+14 | 1.5E+12 | 1.0E+13 |
Volume Resistivity (300 °C) [Ω⋅cm] | 2.5E+13 | 1.0E+13 | 8.3E+06 | 1.0E+06 |
Volume Resistivity (500 °C) [Ω⋅cm] | 5.8E+10 | 1.0E+10 | 8.8E+06 | 1.0E+03 |
Dielectric Constant (1MHz) | 9.9 | 9.9 | 33.7 | 33.0 |
Dielectric Loss Tangent (1MHz) [x10⁻⁴] | <1 | 1 | 17 | 16 |