F-Molding
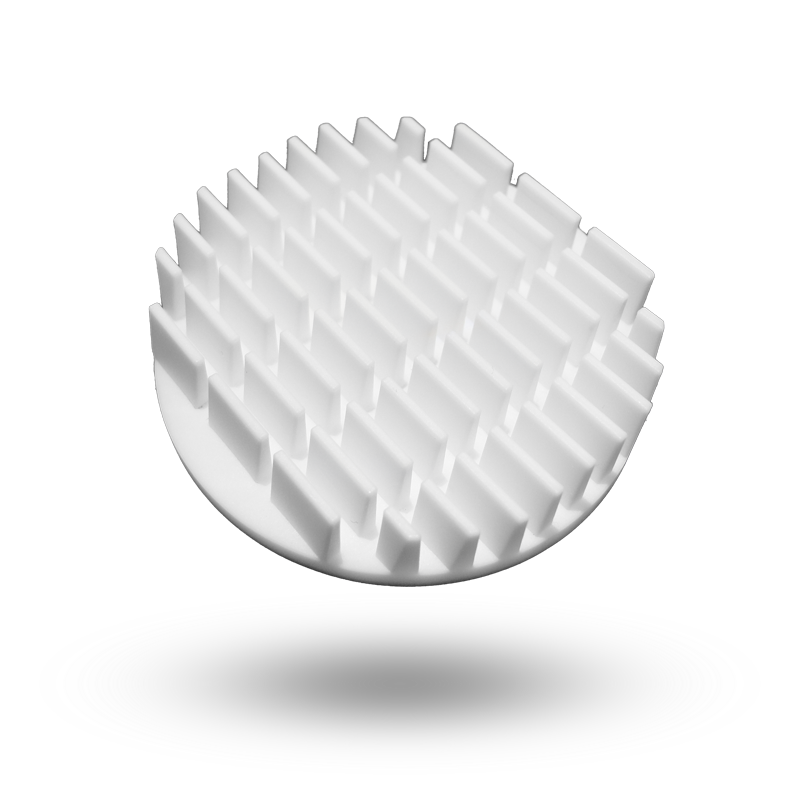
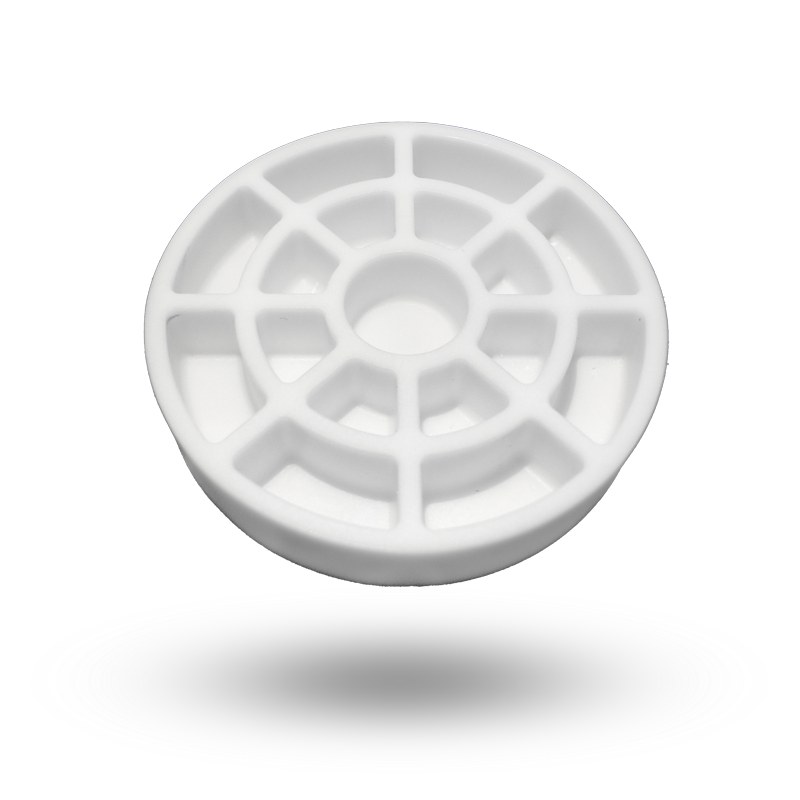
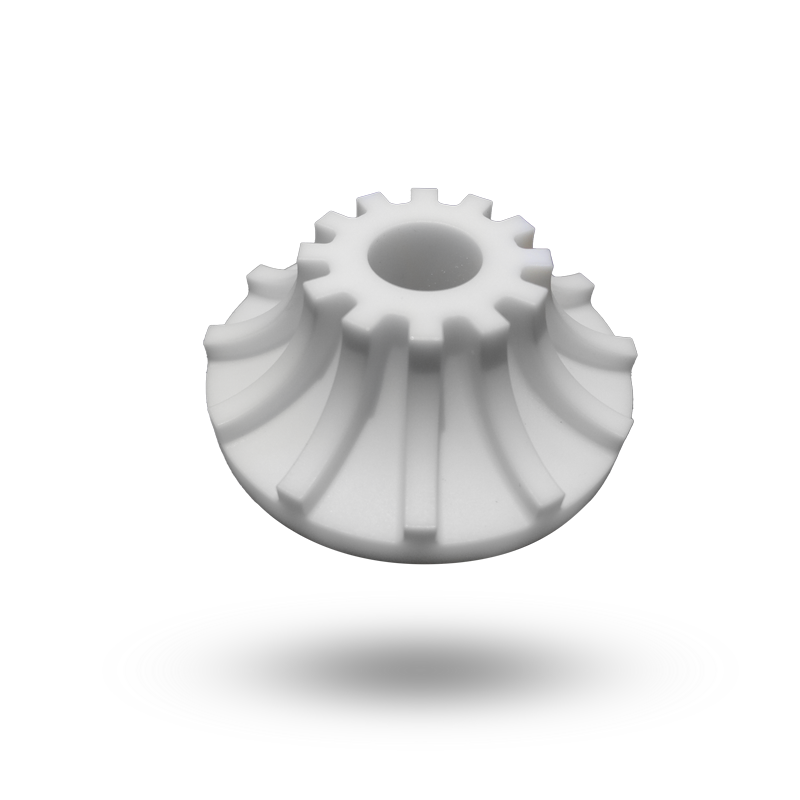
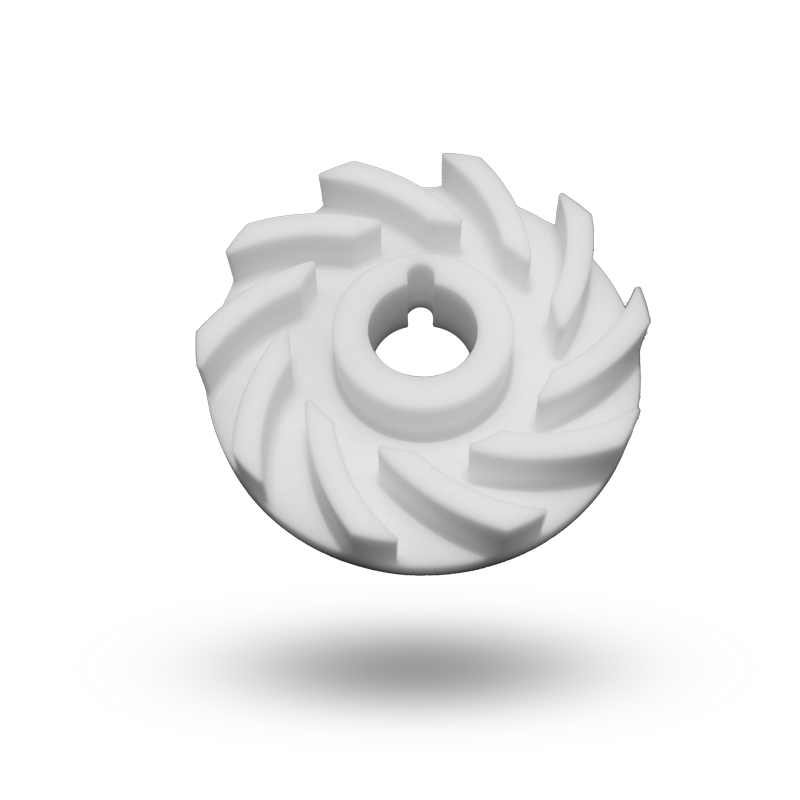
Large dimensions, high complexity and advanced ceramic materials – this is Kyocera‘s new F-Molding technology. This recently developed shaping method combines the high flexibility of additive manufacturing with the capability to produce large components like conventional slip casting. Kyocera already implemented several high-performance materials which can now be shaped by F-Molding:
Material | Zirconia | Cordierite | Silicon Nitride | ||||
---|---|---|---|---|---|---|---|
Material Code | ZO206N | CO220O | CO720O | SN240O | |||
Color | - | White | Gray | Gray | Black | ||
Density | g/cm3 | 6.0 | 2.50 | 2.54 | 3.3 | ||
Mechanical Characteristics | Vickers Hardness HV9.807N | GPa | 12.0 | 8.0 | 8.5 | 14.0 | |
Flexural Strength (3-point Bending) | MPa | 1,100 | 190 | 200 | 1,020 | ||
Young’s Modulus | GPa | 210 | 140 | 145 | 300 | ||
Poisson’s Ratio | - | 0.32 | 0.31 | 0.31 | 0.28 | ||
Fracture Toughness (SEPB) | MPa・m1/2 | 6 | 1-1.5 | 1-1.5 | 7 | ||
Thermal Characteristics | Coefficient of Linear Thermal Expansion | 40-400°C | × 10-6/K | 10.4 | (*) 1.5 | (*) 1.5 | 2.8 |
40-800°C | 10.8 | (*) 2.1 | (*) 2.1 | 3.3 | |||
Thermal Conductivity | 20°C | W/ (m・K) | 3 | 4 | 4 | 27 | |
Specific Heat Capacity | J/ (g・K) | 0.44 | 0.71 | 0.74 | 0.65 | ||
Thermal Shock Resistance (quenching into water) | °C | 300 | 450 | 400 | 800 |
* <|0.05|(23°C), <|0.02|(22°C)
Values are based on typical material properties and may vary according to product configuration and manufacturing process.
Material properties and overall quality are practically the same as for conventionally produced parts (by e.g. pressing). Kyocera utilizes special casting-mold and -core materials, combined with a highly advanced slurry basis, which all were developed and refined in-house to enable high complexity shapes and inner structures and channels.
Near-net shape forming and low setup costs make this a viable shaping method for both prototypes and small series.
Benefits:
- Complex shapes (not possible by machining) and large size possible
- Near-net shape, no hard-machining necessary
- Low setup costs (compared to e.g. pressing or injection molding)
- Material properties equivalent to conventional shaping methods (e.g. pressing)
- Several high-performance materials available